瑞吉特化工设备智能监测系统
客户需求
建设目标
化工厂计划建设化工设备智能监测系统,实现对现场生产设备的运行状态、能耗、环境监测、视频监控等集中管理。该系统将采集设备数据、提供本地及远程监测能力,提升生产管理效率,保障生产安全,优化能耗管理。
边缘端软硬一体工作站对接现场PLC、传感器等设备,实时采集生产数据,并在本地展示关键数据,同时远程传输至物联网监测平台,便于管理人员实时掌控工厂运行情况。
阶段目标
1. 厂内测试阶段:在工厂内部署系统并进行通讯调试,确保各类设备数据正常采集与存储。
2. 现场部署阶段:在生产车间正式安装设备,对接工艺数据,确保系统稳定运行。
3. 远程监测优化:完成平台数据可视化配置,提供设备运行监测、告警分析、数据存储、能耗管理等应用服务。
建设内容
整体架构
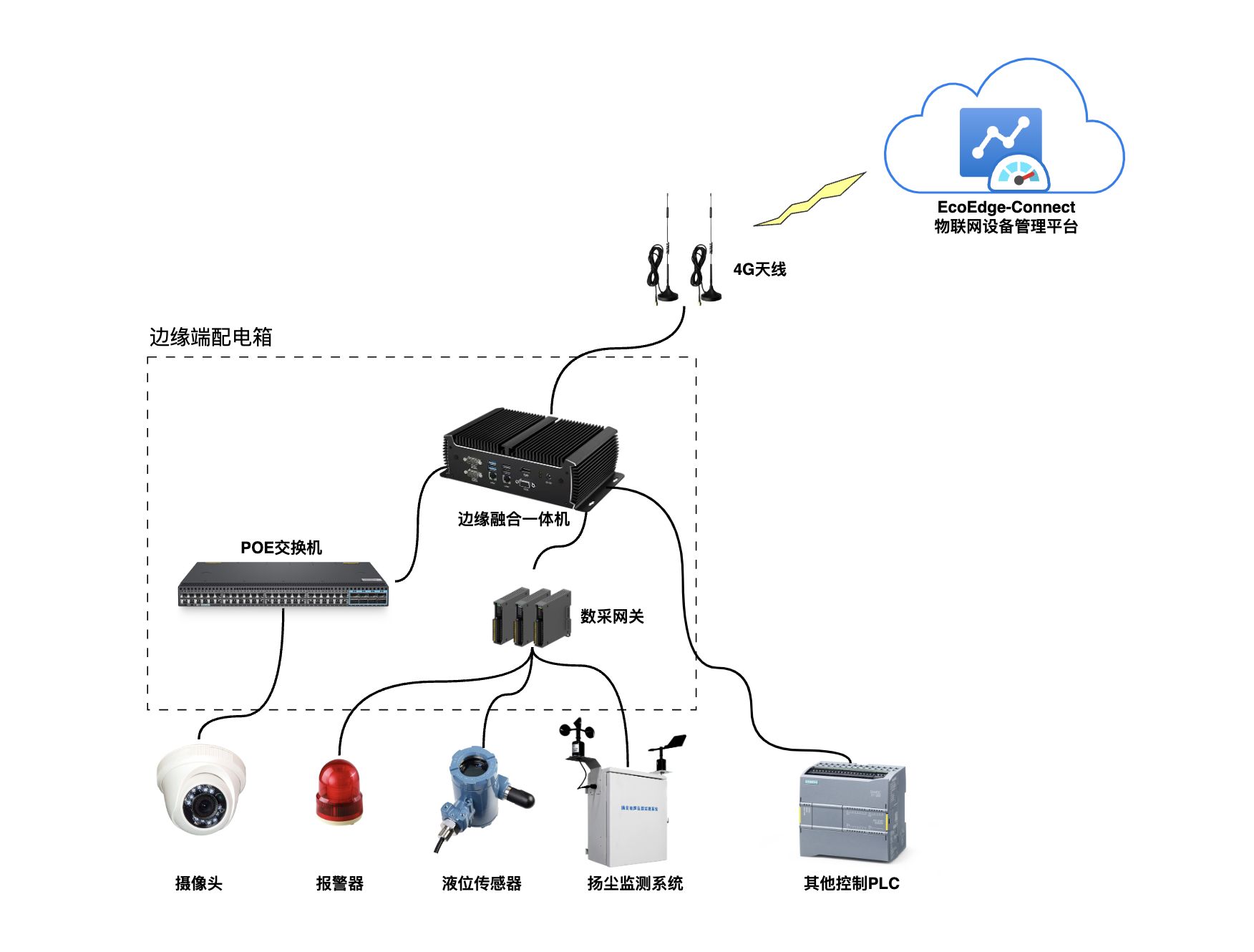
边缘端是整个化工厂智能监测系统的核心组件,负责数据采集、预处理、本地展示及远程传输。其主要功能包括:
• 采集生产设备参数(如温度、压力、流量、液位、能耗等)
• 监测车间环境(如可燃气体浓度、粉尘浓度、温湿度等)
• 采集视频监控数据(对关键工艺流程、设备运行状态进行监控)
• 本地数据存储与展示(仪表板大屏实时展示关键参数、运行曲线)
• 远程数据传输(支持2/3/4G网络,将数据推送至物联网平台)
• 智能告警与安全防护(本地与远程异常报警、设备维保提醒)
• 远程管理与运维(支持远程配置、软件升级)
功能架构
根据化工行业特点,系统的软件架构主要包括:
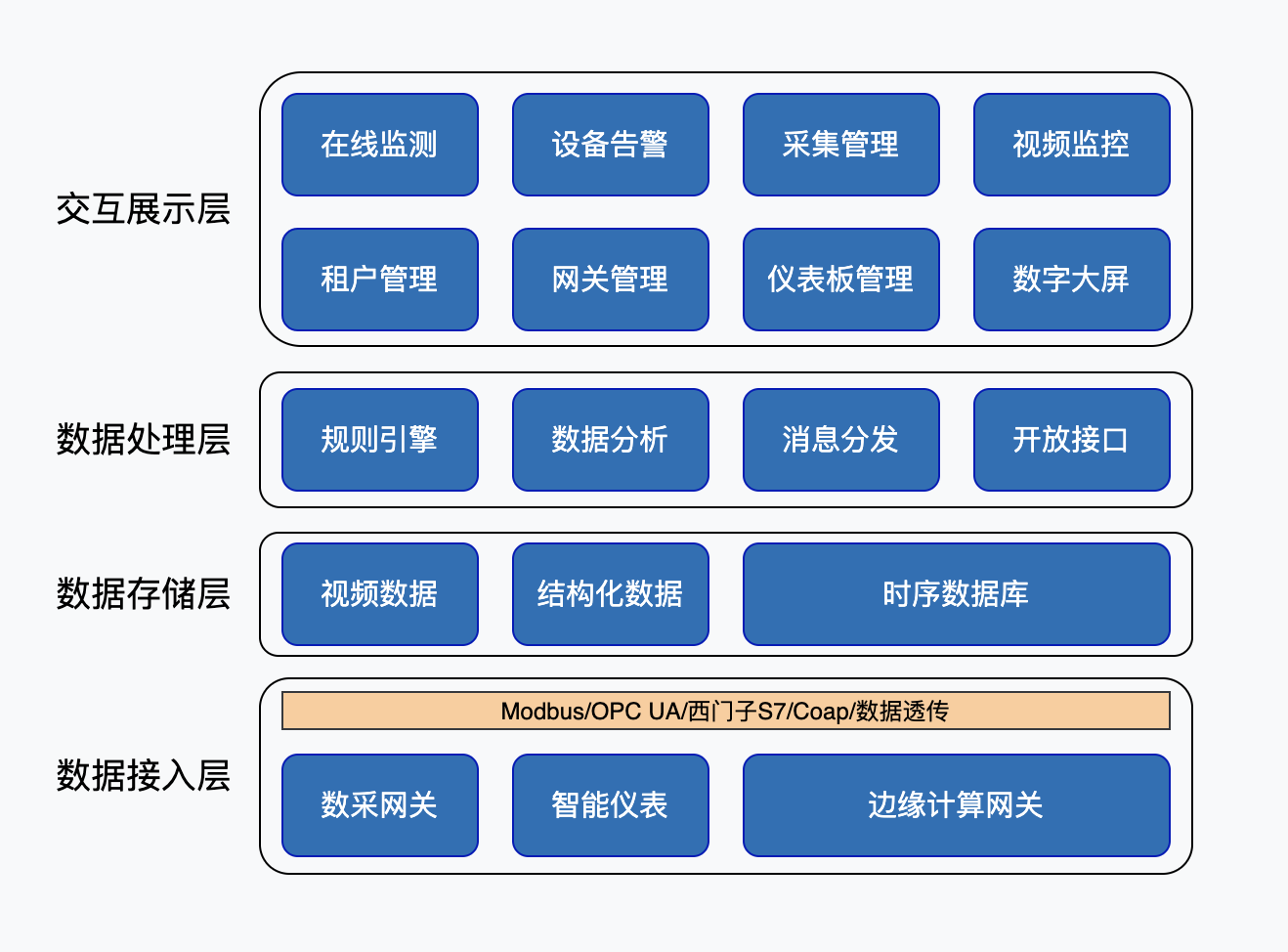
主要功能有:
1. 数据采集接入
• 采集温度、压力、流量、液位、振动、电能、气体浓度等工艺参数
• 采集设备控制系统(PLC/DCS)的运行数据
• 采集生产车间环境数据(粉尘、可燃气体、有害气体浓度等)
• 采集监控视频数据(支持高清摄像头接入)
2. 数据存储与处理
• 采用本地数据库存储2个月的运行数据
• 采用边缘计算框架进行数据清洗、预处理,减少数据传输压力
3. 数据服务
• 异常监测与报警(超温、超压、泄漏、设备故障等)
• 能耗分析(设备能耗对比、单位产量能耗分析)
• 视频管理(录像存储7-15天,按需推送远程监控流)
• 远程数据同步(通过物联网平台远程查看数据)
4. 交互功能展示
• 触摸屏本地显示设备实时运行状态、告警信息、视频画面
• 支持远程网页端、移动端访问,随时掌握工厂生产状态
硬件方案
硬件架构
系统考虑到化工生产现场环境复杂、设备网络安全需求,采用分层分网架构,确保数据安全与可靠性。
• 局域网1: 生产设备传感器网络(485总线接入温度、压力、流量、能耗传感器)
• 局域网2: 监控视频网络(POE交换机接入高清摄像头)
• 局域网3: 控制系统网络(PLC/DCS与边缘计算设备通信)
• 局域网4: 边缘计算内部网络(本地服务器、数据库、可视化终端)
• 外部网络: 通过4G路由器接入公网,与远程物联网平台通讯
核心硬件设备
• 数采网关: 采集生产设备数据,接入温度、压力、流量、气体传感器等
• 视频流媒体服务器: 采集并管理车间监控视频数据,支持存储与远程查看
• 边缘计算一体机: 进行数据处理、分析,内置仪表板实时显示监测数据
• 4G物联网卡: 连接公网,支持边缘网关远程数据传输和远程管理
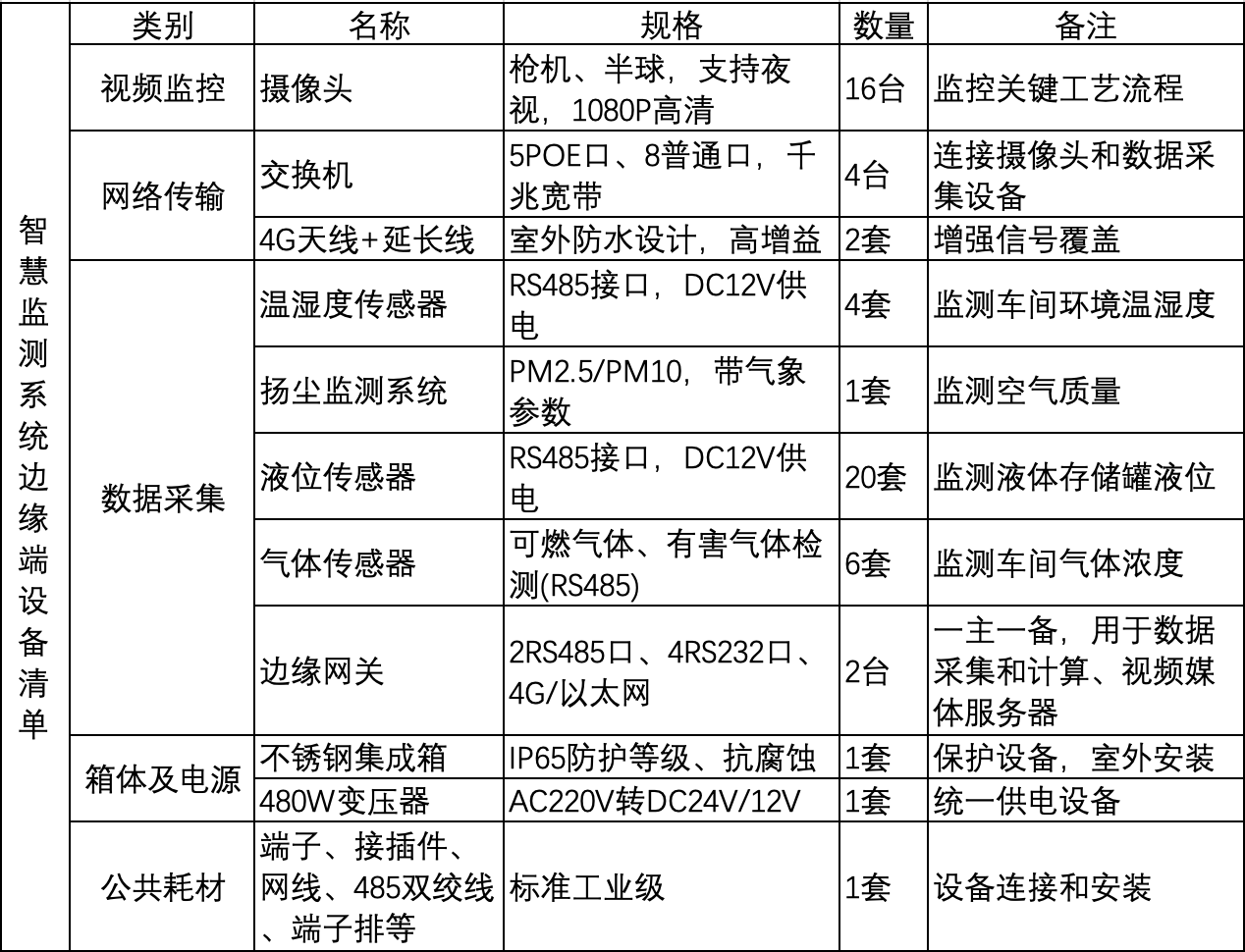
方案亮点
✅ 全方位监测:支持生产设备、能耗、环境、安全、视频等多维度数据采集
✅ 本地+远程融合:本地仪表板大屏实时监测 + 远程平台智能分析
✅ 高效数据存储与分析:支持边缘计算预处理,减少数据传输压力
✅ 智能告警与安全管理:异常数据实时预警,提高工厂安全性
✅ 模块化设计,灵活扩展:支持后续增加新设备、新监测点
客户价值
• 提升生产安全性:实时监测化工厂关键工艺参数,降低安全事故风险
• 优化能耗管理:分析各设备能耗,降低不必要的能源损耗
• 提高生产效率:提供智能监测、报警与远程管理,提高设备运维效率
• 助力数字化转型:构建化工厂智能监测系统,推动智能化升级